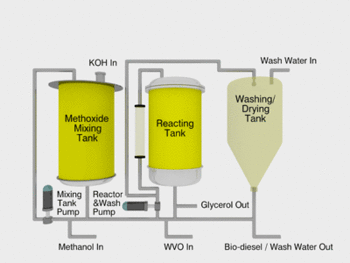
The process of making biodiesel is as follows: Initially, waste vegetable oil is loaded into the reactor and preheated to 55° C (about 131° F). While the oil is preheating, the oil quality is tested for the free fatty acid content by titration with potassium hydroxide (KOH). If the oil quality is satisfactory, the process is continued. A methoxide solution is made by dissolving approximately ten gallons of methanol in approximately five pounds of KOH, and once the oil has reached the required temperature, the methoxide is slowly added and the mixture is agitated for approximately 90 minutes while keeping the temperature constant. After the reaction is over, the reaction mixture is tested to ensure that the reaction has completed.
If the reaction is complete, the reaction mixture is allowed to settle for approximately 12 hours. During this time, crude glycerol, containing fatty acids, methanol, and biodiesel separates from the oil and will settle to the bottom (phase), as its density is greater than the biodiesel (top phase). Both phases do not mix because glycerol at the bottom phase is polar, and biodiesel at the top phase is non-polar. After the settling time has passed, the glycerol is seperated from the biodiesel by gravitational flow (draining from the bottom of the reactor). The separated glycerol is stored in a tank for methanol recovery (remove excess methanol). The biodiesel phase is loaded into the separation tank, where it is washed with water to remove the KOH initially added as a catalyst of the reaction. The washing is repeated several times, until the water runs clear. Once the biodiesel is washed, it is dried to remove any moisture present. The biodiesel is run through the drying process until it passes a drying test. Finally, the dried biodiesel is filtered and stored in the appropriate barrels for consumption.